Factors Affecting the Efficiency of Rock Drilling Tools
Oct 22, 2024
In addition to the correct choice of carbide grade, the efficiency of rock drilling is influenced by many factors, mainly the shape of the drill head, the hardness of the rock, the compressed air pressure, the method of powder discharge, the diameter of the borehole and the depth of the borehole.
Taper Drill Bit Head shape
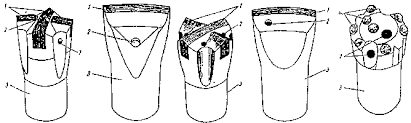
The shape of the drill bit head affects the shape and cross-section of the borehole. The majority of borehole sections are polygons, rather than circles. The lack of roundness is even more pronounced when using large diameter drill heads. The shape of the unrounded hole increases the length of the cut at the base of the eye and the perimeter, and the rock around the base of the eye is hard to break. The speed of drilling is largely influenced by the condition of the well. The non-round holes also hinder the normal rotation of the drill head For deeper holes, the effect is even greater and can even cause twisting of the rod or cause a jam. Recent research has been conducted in an effort to find solutions for some of the problems caused by unrounded holes. Some ways to improve the drilling performance of a drill bit include changing the shape of the drill head, thickening the thickness of the working edge, and increasing the wind pressure. However, the problem has not yet been solved completely, and more research is needed.
Rock Properties
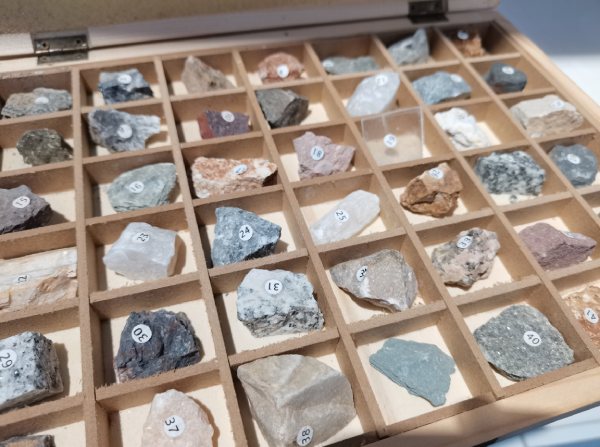
Rock properties that affect drilling speed mainly include cohesiveness, hardness and elasticity. The cohesion of rock is the ability of the rock to resist breaking into smaller pieces. The cohesion of a rock is related to its composition, particle size and shape, cement content, and moisture level. Dense and homogeneous rocks have the same viscosity in all directions, while heterogeneous or laminated rocks have different viscosities in all directions. The hardness of a rock is determined by the connection forces between the rock particles. A rock's hardness, however, is its ability to withstand sharp tools driving into it The elasticity of a rock is how well it returns to its original shape and volume after the external forces acting on it have stopped. All rocks are elastic, which means they stretch and change shape when they are hit or pulled. This affects the efficiency of rock drilling, which is why it is important to take into account the elasticity of the rock when planning an excavation.
Compressed Air Pressure
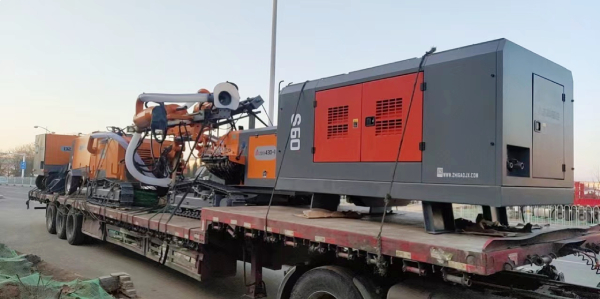
Pressure from compressed air can greatly affect the speed at which drilling is done. The air pressure decreases, and the rate at which the rock drill is supplying rock decreases with it. Several of China's rock drills 01-30, 01-45, 01-38, and YT-25 should have a working pressure of 5 atmospheres or more to ensure normal operation. There are many ways to increase air pressure in order to increase the speed of rock drilling. The general recommendation is that the air pressure should be between 5 and 8 atmospheres. Increased damage to rock drill parts and pipes if too high At a pressure below 5 atmospheres, the rate of drilling of rocks will decrease significantly According to tests, the compressed air consumption during rock drilling is about 7 atmospheres, and the work consumed per unit length of the borehole is minimal at 6 to 6.5 atmospheres.
Rock Powder Removal
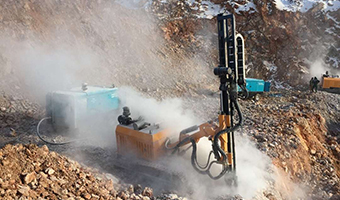
When drilling impact rock, the formation of rock powder in the cannon eye will greatly reduce the supply rate of rock drilling, especially in vertical or inclined rock drilling, the accumulated rock powder, if not excluded in time,It will increase the frequency of crushing and reduce the rock drilling speed There are two main ways to remove rock dust from the gunnel: the blowing method and the water washing method. The blowing method increases the amount of dust in the air, which is harmful to the workers who are operating underground and is now prohibited in underground work. The most common way to clean something is to wash it with water. This method is effective at removing rock dust and helps speed up rock drilling, while also improving working conditions. This method can reduce the amount of dust in the shaft to below 0.2 mg.
Diameter of the Borehole
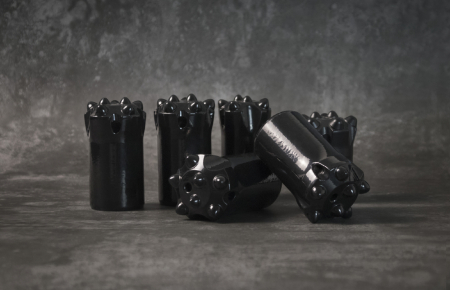
The smaller the diameter of the borehole, the slower the drilling speed. The speed at which the drill bit is rotated can be increased by decreasing the diameter of the drill bit. Drilling speed more than doubles when drilling diameter is increased from 40mm to 60mm When the diameter of the borehole increases, the size of the package used to deliver the water decreases. The increased size of the package can help to improve the rate of use of the borehole, the explosives can be completely detonated, and the blast products and toxic nitrogen oxide levels will be reduced. Tests have shown that using a 40mm pack instead of a standard pack can reduce eye work surface by about 33.3% and increase eye utilization by 15%, as well as other blasting conditions. Explosive material consumption reduced by 42% and explosive consumption reduced by 13%.
Blasthole Depth
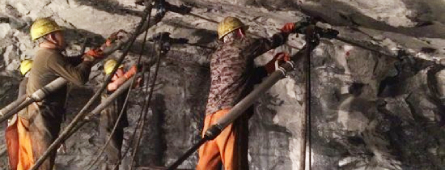
The depth of the blasthole affects how quickly the machine can move forward and how long it will take to complete the work cycle. The hole is deeper and the drilling speed is slowed. As the drill rod's impact energy decreases with increasing depth, the drill's elastic deformation and increased friction cause the loss of drilling efficiency. Changes in blast hole depth cause changes in rock drilling speed Different rocks are harder than others. In harder rocks, the presence of minerals does not have a large effect. Generally speaking, when the air pressure is sufficient, the blasthole depth is below 3 to 3.5 meters, and the drilling speed doesn't change much. According to the test, the drill bits' performance when drilling into different rocks varied depending on their carbide material.
Taper Drill Bit Head shape
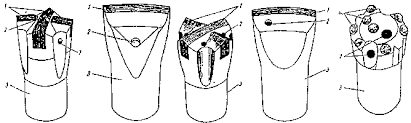
The shape of the drill bit head affects the shape and cross-section of the borehole. The majority of borehole sections are polygons, rather than circles. The lack of roundness is even more pronounced when using large diameter drill heads. The shape of the unrounded hole increases the length of the cut at the base of the eye and the perimeter, and the rock around the base of the eye is hard to break. The speed of drilling is largely influenced by the condition of the well. The non-round holes also hinder the normal rotation of the drill head For deeper holes, the effect is even greater and can even cause twisting of the rod or cause a jam. Recent research has been conducted in an effort to find solutions for some of the problems caused by unrounded holes. Some ways to improve the drilling performance of a drill bit include changing the shape of the drill head, thickening the thickness of the working edge, and increasing the wind pressure. However, the problem has not yet been solved completely, and more research is needed.
Rock Properties
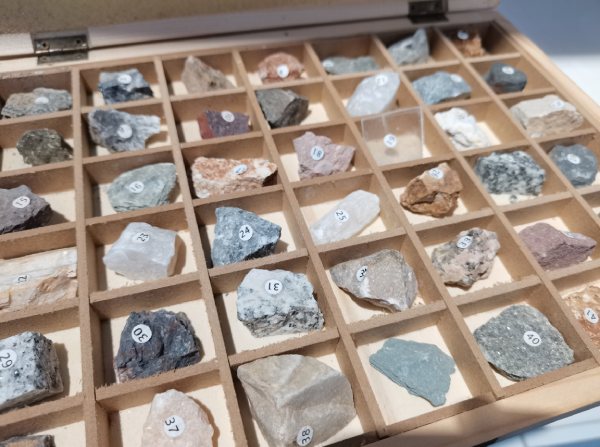
Rock properties that affect drilling speed mainly include cohesiveness, hardness and elasticity. The cohesion of rock is the ability of the rock to resist breaking into smaller pieces. The cohesion of a rock is related to its composition, particle size and shape, cement content, and moisture level. Dense and homogeneous rocks have the same viscosity in all directions, while heterogeneous or laminated rocks have different viscosities in all directions. The hardness of a rock is determined by the connection forces between the rock particles. A rock's hardness, however, is its ability to withstand sharp tools driving into it The elasticity of a rock is how well it returns to its original shape and volume after the external forces acting on it have stopped. All rocks are elastic, which means they stretch and change shape when they are hit or pulled. This affects the efficiency of rock drilling, which is why it is important to take into account the elasticity of the rock when planning an excavation.
Compressed Air Pressure
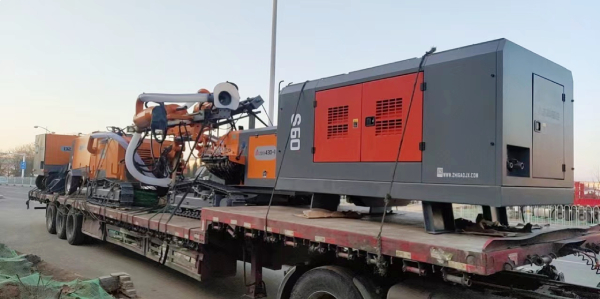
Pressure from compressed air can greatly affect the speed at which drilling is done. The air pressure decreases, and the rate at which the rock drill is supplying rock decreases with it. Several of China's rock drills 01-30, 01-45, 01-38, and YT-25 should have a working pressure of 5 atmospheres or more to ensure normal operation. There are many ways to increase air pressure in order to increase the speed of rock drilling. The general recommendation is that the air pressure should be between 5 and 8 atmospheres. Increased damage to rock drill parts and pipes if too high At a pressure below 5 atmospheres, the rate of drilling of rocks will decrease significantly According to tests, the compressed air consumption during rock drilling is about 7 atmospheres, and the work consumed per unit length of the borehole is minimal at 6 to 6.5 atmospheres.
Rock Powder Removal
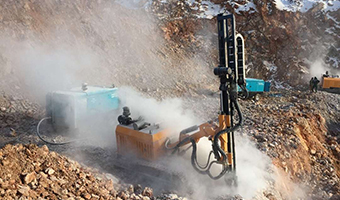
When drilling impact rock, the formation of rock powder in the cannon eye will greatly reduce the supply rate of rock drilling, especially in vertical or inclined rock drilling, the accumulated rock powder, if not excluded in time,It will increase the frequency of crushing and reduce the rock drilling speed There are two main ways to remove rock dust from the gunnel: the blowing method and the water washing method. The blowing method increases the amount of dust in the air, which is harmful to the workers who are operating underground and is now prohibited in underground work. The most common way to clean something is to wash it with water. This method is effective at removing rock dust and helps speed up rock drilling, while also improving working conditions. This method can reduce the amount of dust in the shaft to below 0.2 mg.
Diameter of the Borehole
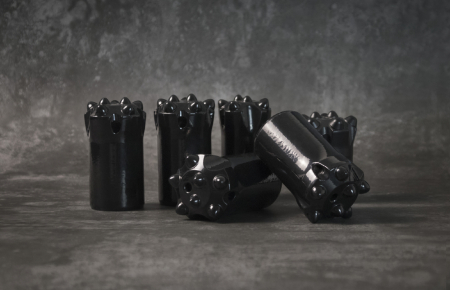
The smaller the diameter of the borehole, the slower the drilling speed. The speed at which the drill bit is rotated can be increased by decreasing the diameter of the drill bit. Drilling speed more than doubles when drilling diameter is increased from 40mm to 60mm When the diameter of the borehole increases, the size of the package used to deliver the water decreases. The increased size of the package can help to improve the rate of use of the borehole, the explosives can be completely detonated, and the blast products and toxic nitrogen oxide levels will be reduced. Tests have shown that using a 40mm pack instead of a standard pack can reduce eye work surface by about 33.3% and increase eye utilization by 15%, as well as other blasting conditions. Explosive material consumption reduced by 42% and explosive consumption reduced by 13%.
Blasthole Depth
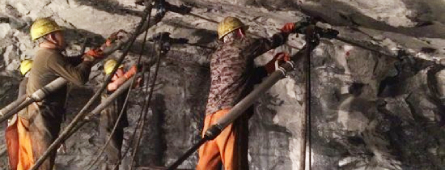
The depth of the blasthole affects how quickly the machine can move forward and how long it will take to complete the work cycle. The hole is deeper and the drilling speed is slowed. As the drill rod's impact energy decreases with increasing depth, the drill's elastic deformation and increased friction cause the loss of drilling efficiency. Changes in blast hole depth cause changes in rock drilling speed Different rocks are harder than others. In harder rocks, the presence of minerals does not have a large effect. Generally speaking, when the air pressure is sufficient, the blasthole depth is below 3 to 3.5 meters, and the drilling speed doesn't change much. According to the test, the drill bits' performance when drilling into different rocks varied depending on their carbide material.