DMiningwell Analysis of the production process of DTH down-the-hole drill(Part 1)
Feb 26, 2025
The origin of MININGWELL can be traced back to 2001. At the beginning, it was a supplier specializing in the production of accessories for drilling rig factories. During the 20-year production and operation process, MININGWELL has its own drilling rig, DTH hammer, and drill pipe production workshops. Its drilling rig brand HUNTER, drilling tool brands SHANTEROCK, D MININGWELL have been loved by many mining areas at domestic and abroad.This article will give you a comprehensive and detailed introduction to the production process and procedures of DMiningwell down-the-hole drills. DMiningwell is committed to creating a transparent factory, customized technical support, real-time customer supervision, and a strict business integration factory for product quality control.
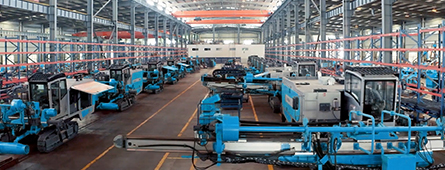
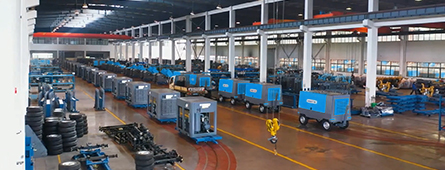
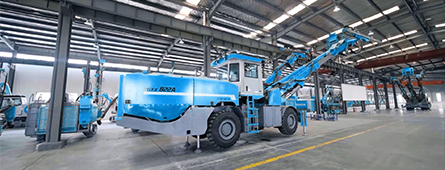
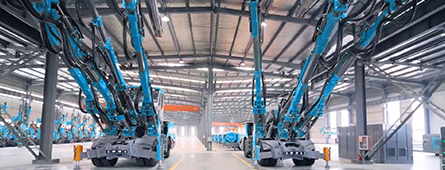
1. Design planning
Demand analysis: Before producing a down-the-hole drill, the manufacturer must first communicate with the customer in depth to understand the customer's specific needs for the drill in different application scenarios (such as mining, infrastructure, water conservancy projects, etc.), including key parameters such as drilling diameter, depth, working environment, and drilling speed. At the same time, it is also necessary to study the advantages and disadvantages of existing products on the market and analyze the development trend of the industry as the basis for design.
Scheme design: Based on the results of the demand analysis, the engineering team begins to design the overall scheme of the drill. This includes determining the mechanical structure of the drill (such as crawler, tire, vehicle-mounted, etc.), power system configuration (selecting the appropriate engine brand, model and power), hydraulic system principle (determining the specifications and parameters of key hydraulic components such as oil pumps, cylinders, control valves, etc.) and the architecture of the electrical control system (design automation level, operation interface layout, etc.). During the design process, computer-aided design (CAD) software will be used to draw detailed two-dimensional drawings and three-dimensional models, accurately design the shape, size, and assembly relationship of each component, and optimize the design scheme through computer simulation analysis to ensure that the drill achieves the best balance in performance, reliability, and ease of operation.
Drawing review and improvement: After completing the preliminary design plan, internal experts, technicians and relevant departments are organized to review the drawings. The review covers multiple aspects such as design rationality, safety, manufacturability, and cost control. For problems and suggestions found in the review, the engineering team will promptly modify and improve them to ensure the accuracy and completeness of the design drawings, providing a reliable basis for subsequent production and manufacturing.
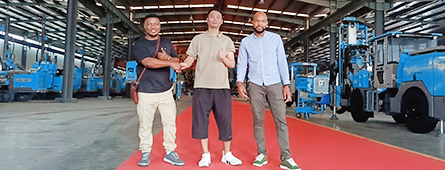
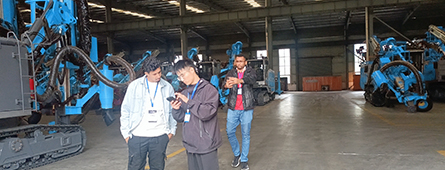
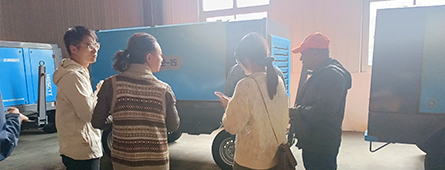
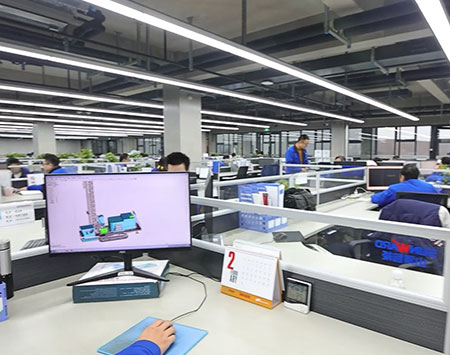
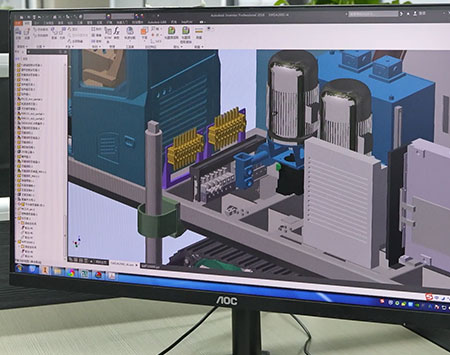
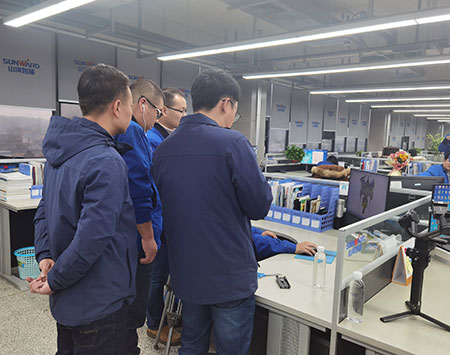
2. Raw material procurement
Raw material selection: According to the design requirements, carefully select raw materials that meet the quality standards. For the main structural parts of the drilling rig, such as the frame, drill arm, propulsion beam, etc., high-strength alloy steel is usually selected to ensure that it can maintain good structural strength and stability when subjected to huge pressure and vibration. Key components, such as engines, hydraulic pumps, motors, reducers, etc., purchase products from well-known brands. These brand products have been verified by the market for a long time and have good performance and reliability, which can provide strong guarantees for the overall performance of the drilling rig. In addition, for some vulnerable parts, such as drill bits, drill rods, seals, etc., high-quality wear-resistant materials will also be selected to extend their service life and reduce customers' use costs.
Supplier evaluation and selection: Establish a strict supplier evaluation system and conduct a comprehensive investigation of potential suppliers. The evaluation content includes the supplier's production capacity, quality control system, product quality stability, delivery guarantee ability, after-sales service level and price competitiveness. Through comparative analysis of multiple suppliers, select the most suitable supplier to establish a long-term cooperative relationship. During the cooperation process, continue to supervise and manage suppliers, and regularly conduct random inspections of the raw materials they supply to ensure that the quality of raw materials always meets the requirements.
Raw material inspection and warehousing: After the raw materials arrive, they will first be strictly inspected by the quality inspection department according to relevant standards and inspection specifications. For raw materials such as steel, chemical composition analysis, mechanical property tests (such as tensile tests, impact tests, etc.) and appearance quality inspections will be carried out to ensure that their materials and performance meet the design requirements. For purchased parts, dimensional accuracy tests and performance tests will be carried out. Only raw materials and parts that pass the inspection can go through the warehousing procedures and enter the production link. For unqualified products, communicate with suppliers in a timely manner to return or exchange them. It is strictly forbidden for unqualified raw materials to enter the production process to ensure product quality from the source.
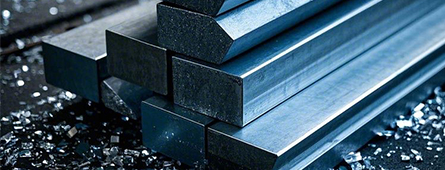
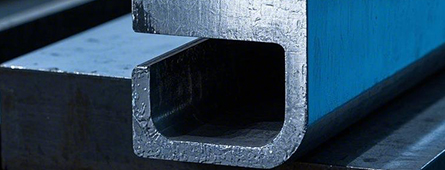
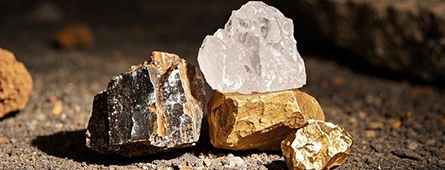
3. Parts processing
Cutting and blanking: According to the size requirements of the design drawings, the purchased steel is cut and blanked by various cutting equipment. Common cutting methods include flame cutting, plasma cutting, laser cutting, etc. For plates with simple shapes and large sizes, flame cutting is generally used; for plates with high precision requirements and thin thickness, plasma cutting or laser cutting is used. The cut materials will be edge-grinded to remove burrs and scales generated by cutting, ensure accurate blanking size and smooth edges, and prepare for subsequent processing procedures.
Mechanical processing: After blanking, the parts enter the mechanical processing workshop, and through various mechanical processing processes such as turning, milling, boring, and grinding, the shape, size, surface roughness, etc. of the parts are precisely processed to meet the requirements of the design drawings. For example, for key parts such as engine mounting seats and hydraulic cylinder mounting holes, high-precision boring processing is required to ensure installation accuracy; for transmission parts such as transmission shafts and gears, turning and grinding are required to ensure their dimensional accuracy and surface finish to reduce wear and noise during transmission. During the machining process, high-precision CNC machine tools and advanced tools are used, and strict quality control measures are adopted, such as first-piece inspection, process inspection, and final inspection, to ensure that the processing quality of each component meets the standards.
Welding and assembly: Some of the mechanically processed parts need to be welded and assembled into larger parts. The welding process plays a vital role in the production of down-the-hole drills, which directly affects the structural strength and stability of the drills. For welders, professional welding skills and qualifications are required, and they must operate in strict accordance with the welding process regulations. During the welding process, appropriate welding methods (such as manual arc welding, carbon dioxide gas shielded welding, submerged arc welding, etc.) and welding materials are used, and the welding parameters are precisely controlled. After welding is completed, the weld is visually inspected and non-destructive testing (such as ultrasonic testing, radiographic testing, etc.) is performed to ensure that the weld quality is defect-free. For some components composed of multiple parts, such as drill arms, propulsion beams, etc., after welding is completed, overall assembly and debugging are required to ensure that the connection between the components is firm and the matching accuracy meets the requirements.
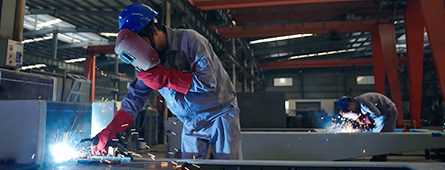
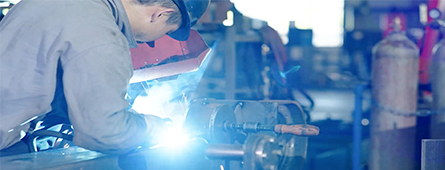
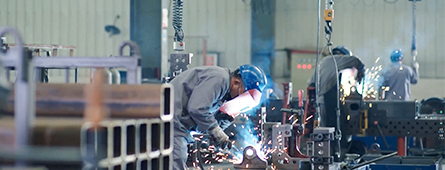
The first part is finished, the second part will be in the next article!
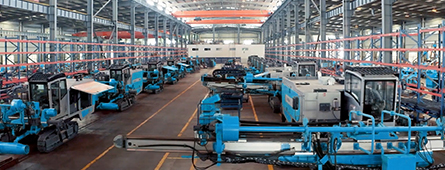
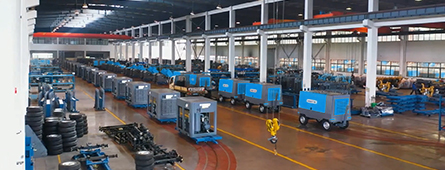
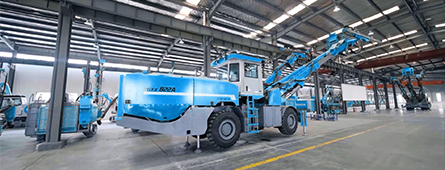
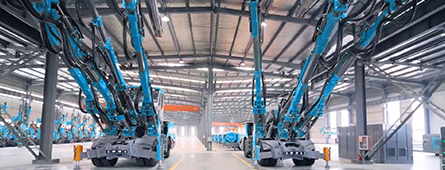
1. Design planning
Demand analysis: Before producing a down-the-hole drill, the manufacturer must first communicate with the customer in depth to understand the customer's specific needs for the drill in different application scenarios (such as mining, infrastructure, water conservancy projects, etc.), including key parameters such as drilling diameter, depth, working environment, and drilling speed. At the same time, it is also necessary to study the advantages and disadvantages of existing products on the market and analyze the development trend of the industry as the basis for design.
Scheme design: Based on the results of the demand analysis, the engineering team begins to design the overall scheme of the drill. This includes determining the mechanical structure of the drill (such as crawler, tire, vehicle-mounted, etc.), power system configuration (selecting the appropriate engine brand, model and power), hydraulic system principle (determining the specifications and parameters of key hydraulic components such as oil pumps, cylinders, control valves, etc.) and the architecture of the electrical control system (design automation level, operation interface layout, etc.). During the design process, computer-aided design (CAD) software will be used to draw detailed two-dimensional drawings and three-dimensional models, accurately design the shape, size, and assembly relationship of each component, and optimize the design scheme through computer simulation analysis to ensure that the drill achieves the best balance in performance, reliability, and ease of operation.
Drawing review and improvement: After completing the preliminary design plan, internal experts, technicians and relevant departments are organized to review the drawings. The review covers multiple aspects such as design rationality, safety, manufacturability, and cost control. For problems and suggestions found in the review, the engineering team will promptly modify and improve them to ensure the accuracy and completeness of the design drawings, providing a reliable basis for subsequent production and manufacturing.
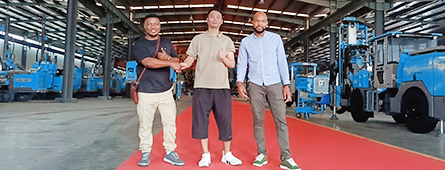
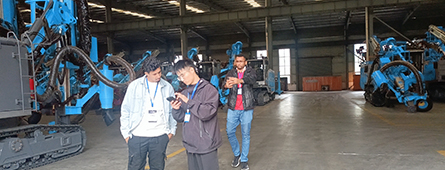
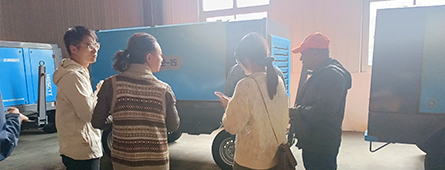
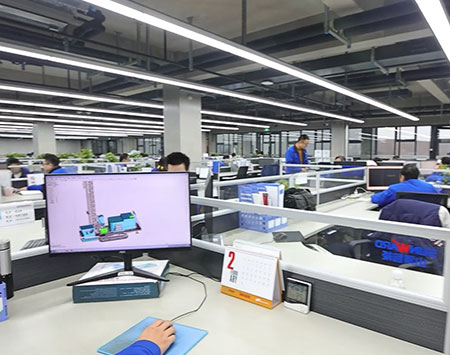
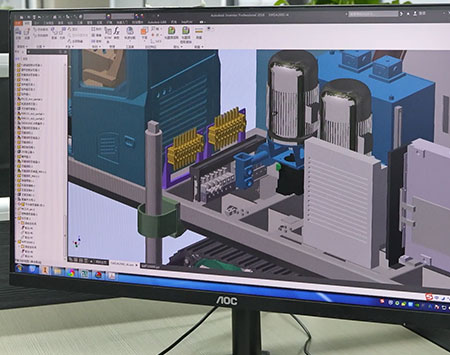
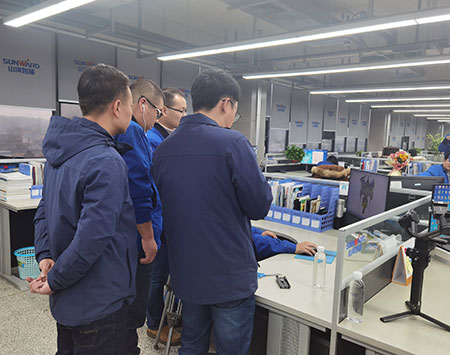
2. Raw material procurement
Raw material selection: According to the design requirements, carefully select raw materials that meet the quality standards. For the main structural parts of the drilling rig, such as the frame, drill arm, propulsion beam, etc., high-strength alloy steel is usually selected to ensure that it can maintain good structural strength and stability when subjected to huge pressure and vibration. Key components, such as engines, hydraulic pumps, motors, reducers, etc., purchase products from well-known brands. These brand products have been verified by the market for a long time and have good performance and reliability, which can provide strong guarantees for the overall performance of the drilling rig. In addition, for some vulnerable parts, such as drill bits, drill rods, seals, etc., high-quality wear-resistant materials will also be selected to extend their service life and reduce customers' use costs.
Supplier evaluation and selection: Establish a strict supplier evaluation system and conduct a comprehensive investigation of potential suppliers. The evaluation content includes the supplier's production capacity, quality control system, product quality stability, delivery guarantee ability, after-sales service level and price competitiveness. Through comparative analysis of multiple suppliers, select the most suitable supplier to establish a long-term cooperative relationship. During the cooperation process, continue to supervise and manage suppliers, and regularly conduct random inspections of the raw materials they supply to ensure that the quality of raw materials always meets the requirements.
Raw material inspection and warehousing: After the raw materials arrive, they will first be strictly inspected by the quality inspection department according to relevant standards and inspection specifications. For raw materials such as steel, chemical composition analysis, mechanical property tests (such as tensile tests, impact tests, etc.) and appearance quality inspections will be carried out to ensure that their materials and performance meet the design requirements. For purchased parts, dimensional accuracy tests and performance tests will be carried out. Only raw materials and parts that pass the inspection can go through the warehousing procedures and enter the production link. For unqualified products, communicate with suppliers in a timely manner to return or exchange them. It is strictly forbidden for unqualified raw materials to enter the production process to ensure product quality from the source.
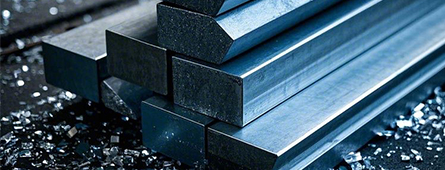
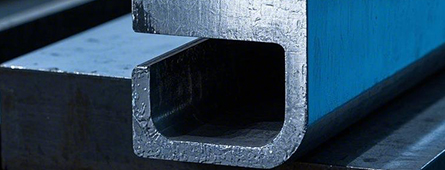
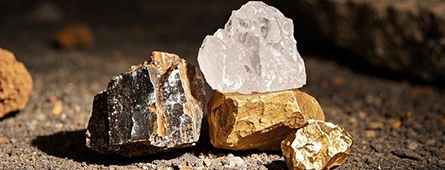
3. Parts processing
Cutting and blanking: According to the size requirements of the design drawings, the purchased steel is cut and blanked by various cutting equipment. Common cutting methods include flame cutting, plasma cutting, laser cutting, etc. For plates with simple shapes and large sizes, flame cutting is generally used; for plates with high precision requirements and thin thickness, plasma cutting or laser cutting is used. The cut materials will be edge-grinded to remove burrs and scales generated by cutting, ensure accurate blanking size and smooth edges, and prepare for subsequent processing procedures.
Mechanical processing: After blanking, the parts enter the mechanical processing workshop, and through various mechanical processing processes such as turning, milling, boring, and grinding, the shape, size, surface roughness, etc. of the parts are precisely processed to meet the requirements of the design drawings. For example, for key parts such as engine mounting seats and hydraulic cylinder mounting holes, high-precision boring processing is required to ensure installation accuracy; for transmission parts such as transmission shafts and gears, turning and grinding are required to ensure their dimensional accuracy and surface finish to reduce wear and noise during transmission. During the machining process, high-precision CNC machine tools and advanced tools are used, and strict quality control measures are adopted, such as first-piece inspection, process inspection, and final inspection, to ensure that the processing quality of each component meets the standards.
Welding and assembly: Some of the mechanically processed parts need to be welded and assembled into larger parts. The welding process plays a vital role in the production of down-the-hole drills, which directly affects the structural strength and stability of the drills. For welders, professional welding skills and qualifications are required, and they must operate in strict accordance with the welding process regulations. During the welding process, appropriate welding methods (such as manual arc welding, carbon dioxide gas shielded welding, submerged arc welding, etc.) and welding materials are used, and the welding parameters are precisely controlled. After welding is completed, the weld is visually inspected and non-destructive testing (such as ultrasonic testing, radiographic testing, etc.) is performed to ensure that the weld quality is defect-free. For some components composed of multiple parts, such as drill arms, propulsion beams, etc., after welding is completed, overall assembly and debugging are required to ensure that the connection between the components is firm and the matching accuracy meets the requirements.
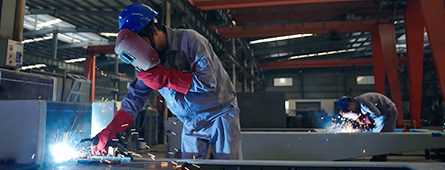
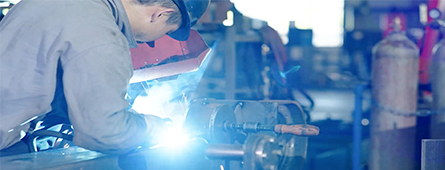
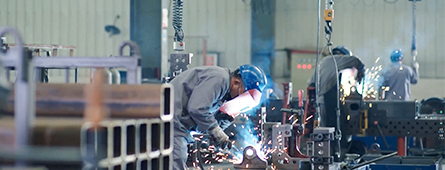
The first part is finished, the second part will be in the next article!