DMiningwell Analysis of the production process of DTH down-the-hole drill(Part 2)
Feb 27, 2025
This article explains in detail parts 1-7 to show customers the rigorous and meticulous production process of DMiningwell DTH drilling
rig. Only then can a down-the-hole drill rig with excellent performance and reliable quality be born, providing a solid guarantee for efficient operations in mining, infrastructure construction and other fields.
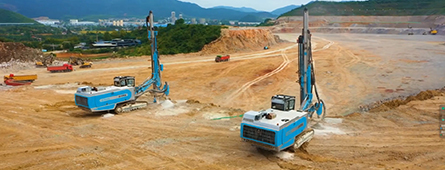
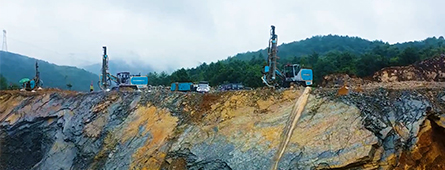
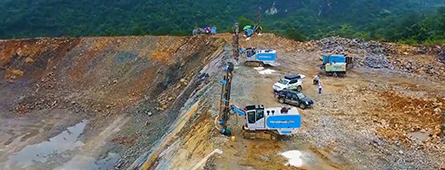
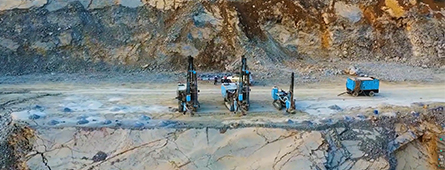
The previous article described the production preparation process of the DMiningwell down-the-hole drill from design to raw material procurement and parts processing. This article will continue to lead everyone to personally participate in how a down-the-hole drill is transformed from scattered parts into a powerful machine through a detailed explanation of part 4-part 7.
4. Component assembly and debugging
Component assembly: The processed and qualified components are transported to the assembly workshop and assembled according to the design drawings and assembly process requirements. During the assembly process, the assembly sequence, assembly clearance and tightening torque of each component are strictly controlled. For example, when installing key components such as engines, hydraulic pumps, and reducers, special installation tools and measuring instruments should be used to ensure that the installation position is accurate and the transmission connection between components is smooth. For some parts that need to be sealed, such as the piston rod seal of the hydraulic cylinder and the oil pipe joint seal, suitable seals should be selected and installed according to the correct installation method to ensure good sealing performance and prevent leakage. During the assembly process, some important assembly links will also be recorded for traceability and quality analysis.
Component debugging: After completing the component assembly, each assembled component will be debugged to check whether its various performance indicators meet the design requirements. For hydraulic system components, pressure tests, flow tests and leakage tests will be performed to adjust the system pressure and flow to ensure that the hydraulic system runs smoothly and without leakage. For electrical system components, electrical performance tests will be conducted to check whether the line connection is correct and whether the electrical components are working properly. The control system parameters will be debugged to ensure accurate and sensitive operation control. For transmission components, no-load and load test runs will be conducted to check whether the transmission is smooth and whether there is abnormal noise and vibration. The clearance and tension of the transmission components will be adjusted to ensure transmission efficiency and reliability. During the debugging process, if any problems are found, they will be promptly checked and rectified until the performance of the components meets the design requirements.
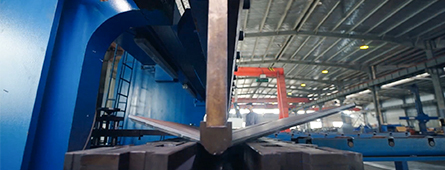
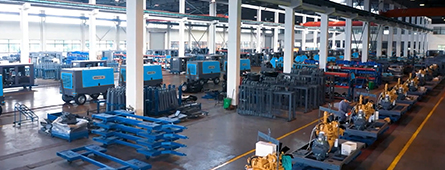
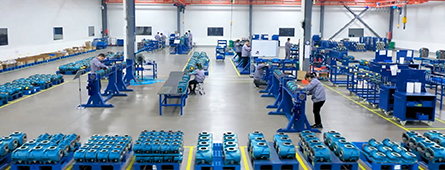
5. Assembly of the whole machine
Building the basic framework: Based on the frame of the drilling rig, first install the chassis walking mechanism (such as crawler chassis, tire chassis, etc.) to ensure that the chassis is firmly installed and runs smoothly. Then, install the main frame structure of the drilling rig on the chassis, including the drill arm support seat, propulsion beam mounting frame, etc. Through precise measurement and adjustment, ensure the position accuracy and verticality between the components, and provide a stable foundation for the subsequent component installation.
Installation of core components: Install the core components such as the engine, hydraulic system, electrical system, slewing mechanism, propulsion mechanism, etc. that have been debugged and qualified on the main frame in turn. During the installation process, strictly follow the assembly process requirements to ensure that the connection between the components is firm and the pipeline and line connections are correct. For example, when installing the hydraulic system, the oil pipes should be reasonably arranged and fixed to avoid crossing, twisting and wear of the oil pipes. At the same time, ensure that the oil pipe joints are well sealed to prevent hydraulic oil leakage. When installing the electrical system, the wires and cables should be neatly routed and tied to ensure that the insulation performance of the electrical lines is good to avoid short circuits and open circuits.
Installation of auxiliary equipment: installation of auxiliary equipment of the drilling rig, such as dust removal system, cooling system, operation console, protective devices, etc. The dust removal system is used to collect dust generated during the drilling process to protect the working environment and the health of operators; the cooling system is used to cool the engine, hydraulic oil, etc. to ensure that the equipment maintains a normal working temperature during long-term operation; the operation console provides operators with a convenient operation interface to achieve various control functions of the drilling rig; the protective device is used to protect the safety of operators and prevent accidents during the operation of the equipment. When installing auxiliary equipment, attention should be paid to the coordination and compatibility between the various equipment to ensure the integrity and reliability of the entire drilling rig system.
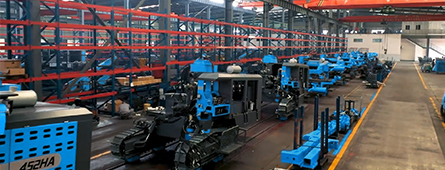
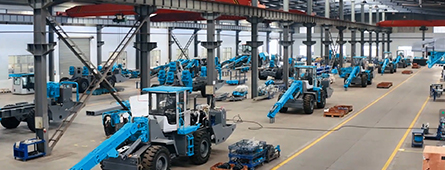
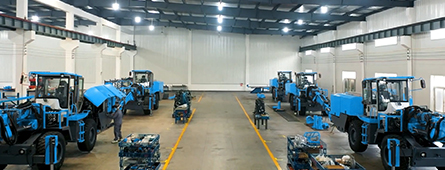
6. Whole machine debugging and testing
No-load debugging: After the whole machine is assembled, no-load debugging is performed first. Start the engine and check whether the parameters such as the engine's starting performance, operating stability and idle speed are normal. Then, the hydraulic system, electrical system, slewing mechanism, propulsion mechanism, etc. are debugged in no-load operation in turn to check whether the movements of each system and mechanism are smooth and accurate, and whether there are abnormal noises and vibrations. During the no-load debugging process, the pressure, flow, speed and other parameters of each system are measured and adjusted to meet the design requirements. At the same time, check whether the various control functions of the operating console are normal, and the operator can conveniently and accurately perform various operations on the drilling rig.
Load debugging: After the no-load debugging is qualified, load debugging is performed. Simulate the working conditions of the drilling rig in actual work, apply a certain load to the drilling rig, such as conducting a drilling test on a drilling test bench, and check the drilling performance, drilling accuracy, stability and other indicators of the drilling rig under load. During the load debugging process, pay close attention to the power output of the engine, the pressure changes of the hydraulic system, the stress conditions of each component, etc., and promptly discover and solve possible problems. Through load debugging, the performance parameters of the drilling rig are further optimized to ensure that the drilling rig can operate stably and efficiently in actual work.
Performance testing and quality inspection: According to relevant national standards, industry standards and quality inspection specifications formulated by the enterprise, the drilling rig is comprehensively tested and inspected. The inspection content includes the drilling diameter, drilling depth, drilling speed, rotary torque, propulsion force, walking speed, climbing ability, noise, vibration, emission and other performance indicators of the drilling rig, as well as appearance quality, assembly quality, safety protection devices and other aspects. Use professional testing equipment and instruments, such as hardness testers, roughness meters, torque wrenches, pressure gauges, flow meters, noise testers, vibration testers, etc., to accurately measure and analyze the various parameters of the drilling rig. Only after strict testing and inspection, the drilling rigs that meet the requirements of various indicators can be judged as qualified products and enter the next link.
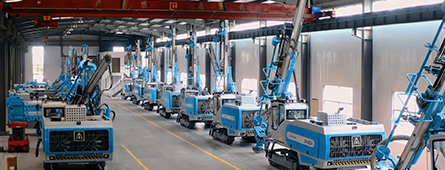
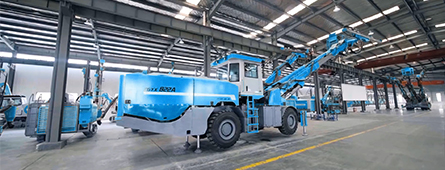
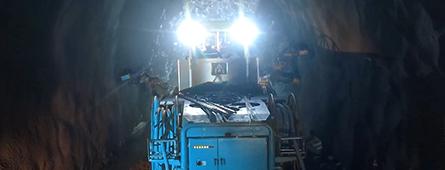
7. Appearance painting and packaging
Appearance painting: The drilling rigs that have passed the inspection are treated with appearance painting to improve the appearance and anti-corrosion performance of the drilling rigs. First, the surface of the drilling rig is pre-treated, and the rust, oil and impurities on the surface are removed by sandblasting, shot blasting, etc., so that the surface reaches a certain roughness and increases the adhesion of the coating. Then, the primer is sprayed. The primer has good anti-rust and corrosion resistance and can provide a good foundation for the subsequent topcoat. After the primer is dry, the topcoat is sprayed. The color and gloss of the topcoat are selected according to customer requirements or corporate standards. Generally, durable and weather-resistant paint is used to ensure that the appearance of the drilling rig remains good during long-term use. During the painting process, the temperature, humidity and ventilation conditions of the painting environment are strictly controlled to ensure that the painting quality meets the standards.
Packaging and transportation: Design a suitable packaging plan according to the size, weight and transportation requirements of the drilling rig. For small down-the-hole drilling rigs, wooden boxes are generally used for packaging, and cushioning materials such as foam boards and air cushion films are set in the wooden boxes to prevent the drilling rigs from being collided and damaged during transportation. For large down-the-hole drilling rigs, it may be necessary to use frame packaging or bare packaging with protection, and use professional transportation vehicles and fixing devices during transportation to ensure the safety of the drilling rig during transportation. The model, specifications, quantity, manufacturer, destination and other information of the drilling rig should be marked on the packaging to facilitate transportation and handover. At the same time, provide customers with detailed transportation lists and product certificates and other relevant documents to ensure that the drilling rig can be smoothly delivered to customers.
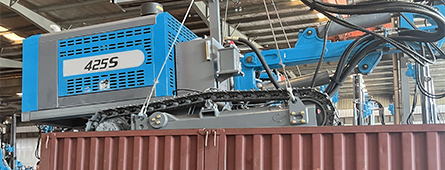
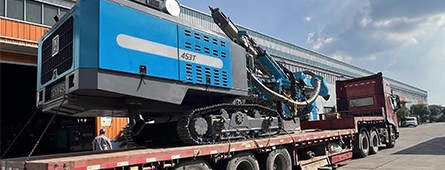
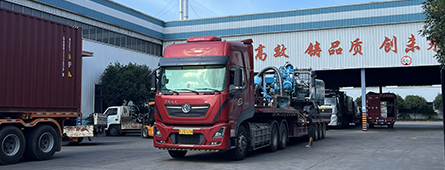
Through the above rigorous and meticulous production process, a down-the-hole drill rig with excellent performance and reliable quality was born, providing a solid guarantee for efficient operations in mining, infrastructure and other fields.
rig. Only then can a down-the-hole drill rig with excellent performance and reliable quality be born, providing a solid guarantee for efficient operations in mining, infrastructure construction and other fields.
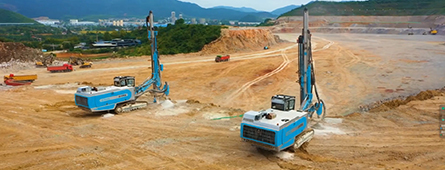
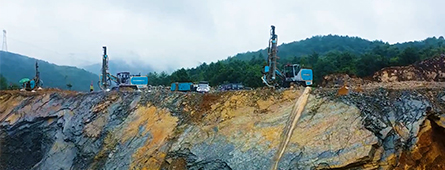
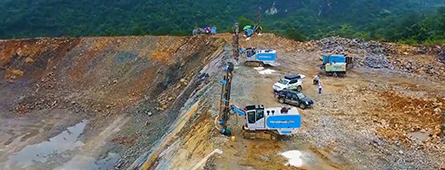
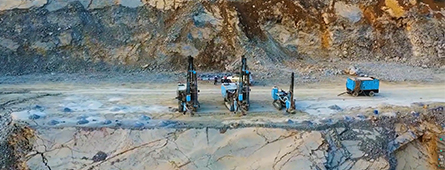
The previous article described the production preparation process of the DMiningwell down-the-hole drill from design to raw material procurement and parts processing. This article will continue to lead everyone to personally participate in how a down-the-hole drill is transformed from scattered parts into a powerful machine through a detailed explanation of part 4-part 7.
4. Component assembly and debugging
Component assembly: The processed and qualified components are transported to the assembly workshop and assembled according to the design drawings and assembly process requirements. During the assembly process, the assembly sequence, assembly clearance and tightening torque of each component are strictly controlled. For example, when installing key components such as engines, hydraulic pumps, and reducers, special installation tools and measuring instruments should be used to ensure that the installation position is accurate and the transmission connection between components is smooth. For some parts that need to be sealed, such as the piston rod seal of the hydraulic cylinder and the oil pipe joint seal, suitable seals should be selected and installed according to the correct installation method to ensure good sealing performance and prevent leakage. During the assembly process, some important assembly links will also be recorded for traceability and quality analysis.
Component debugging: After completing the component assembly, each assembled component will be debugged to check whether its various performance indicators meet the design requirements. For hydraulic system components, pressure tests, flow tests and leakage tests will be performed to adjust the system pressure and flow to ensure that the hydraulic system runs smoothly and without leakage. For electrical system components, electrical performance tests will be conducted to check whether the line connection is correct and whether the electrical components are working properly. The control system parameters will be debugged to ensure accurate and sensitive operation control. For transmission components, no-load and load test runs will be conducted to check whether the transmission is smooth and whether there is abnormal noise and vibration. The clearance and tension of the transmission components will be adjusted to ensure transmission efficiency and reliability. During the debugging process, if any problems are found, they will be promptly checked and rectified until the performance of the components meets the design requirements.
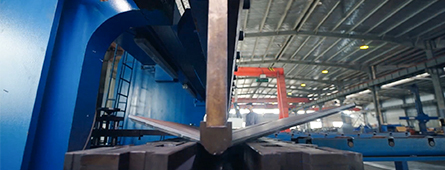
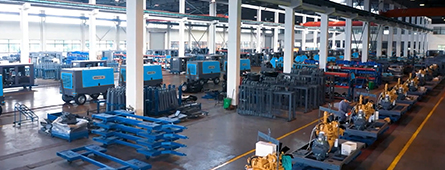
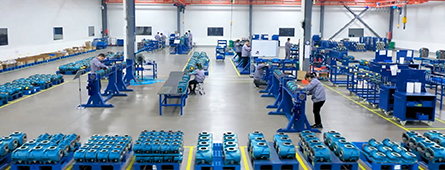
5. Assembly of the whole machine
Building the basic framework: Based on the frame of the drilling rig, first install the chassis walking mechanism (such as crawler chassis, tire chassis, etc.) to ensure that the chassis is firmly installed and runs smoothly. Then, install the main frame structure of the drilling rig on the chassis, including the drill arm support seat, propulsion beam mounting frame, etc. Through precise measurement and adjustment, ensure the position accuracy and verticality between the components, and provide a stable foundation for the subsequent component installation.
Installation of core components: Install the core components such as the engine, hydraulic system, electrical system, slewing mechanism, propulsion mechanism, etc. that have been debugged and qualified on the main frame in turn. During the installation process, strictly follow the assembly process requirements to ensure that the connection between the components is firm and the pipeline and line connections are correct. For example, when installing the hydraulic system, the oil pipes should be reasonably arranged and fixed to avoid crossing, twisting and wear of the oil pipes. At the same time, ensure that the oil pipe joints are well sealed to prevent hydraulic oil leakage. When installing the electrical system, the wires and cables should be neatly routed and tied to ensure that the insulation performance of the electrical lines is good to avoid short circuits and open circuits.
Installation of auxiliary equipment: installation of auxiliary equipment of the drilling rig, such as dust removal system, cooling system, operation console, protective devices, etc. The dust removal system is used to collect dust generated during the drilling process to protect the working environment and the health of operators; the cooling system is used to cool the engine, hydraulic oil, etc. to ensure that the equipment maintains a normal working temperature during long-term operation; the operation console provides operators with a convenient operation interface to achieve various control functions of the drilling rig; the protective device is used to protect the safety of operators and prevent accidents during the operation of the equipment. When installing auxiliary equipment, attention should be paid to the coordination and compatibility between the various equipment to ensure the integrity and reliability of the entire drilling rig system.
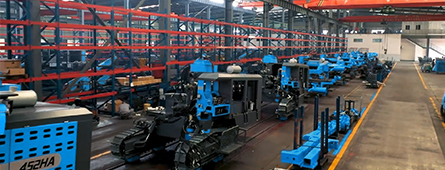
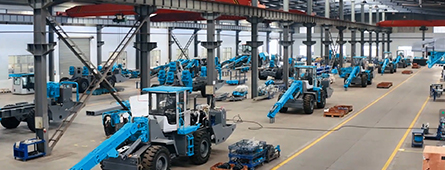
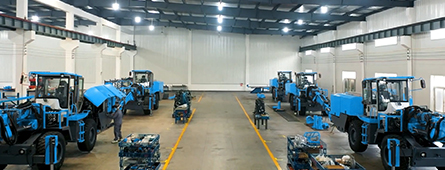
6. Whole machine debugging and testing
No-load debugging: After the whole machine is assembled, no-load debugging is performed first. Start the engine and check whether the parameters such as the engine's starting performance, operating stability and idle speed are normal. Then, the hydraulic system, electrical system, slewing mechanism, propulsion mechanism, etc. are debugged in no-load operation in turn to check whether the movements of each system and mechanism are smooth and accurate, and whether there are abnormal noises and vibrations. During the no-load debugging process, the pressure, flow, speed and other parameters of each system are measured and adjusted to meet the design requirements. At the same time, check whether the various control functions of the operating console are normal, and the operator can conveniently and accurately perform various operations on the drilling rig.
Load debugging: After the no-load debugging is qualified, load debugging is performed. Simulate the working conditions of the drilling rig in actual work, apply a certain load to the drilling rig, such as conducting a drilling test on a drilling test bench, and check the drilling performance, drilling accuracy, stability and other indicators of the drilling rig under load. During the load debugging process, pay close attention to the power output of the engine, the pressure changes of the hydraulic system, the stress conditions of each component, etc., and promptly discover and solve possible problems. Through load debugging, the performance parameters of the drilling rig are further optimized to ensure that the drilling rig can operate stably and efficiently in actual work.
Performance testing and quality inspection: According to relevant national standards, industry standards and quality inspection specifications formulated by the enterprise, the drilling rig is comprehensively tested and inspected. The inspection content includes the drilling diameter, drilling depth, drilling speed, rotary torque, propulsion force, walking speed, climbing ability, noise, vibration, emission and other performance indicators of the drilling rig, as well as appearance quality, assembly quality, safety protection devices and other aspects. Use professional testing equipment and instruments, such as hardness testers, roughness meters, torque wrenches, pressure gauges, flow meters, noise testers, vibration testers, etc., to accurately measure and analyze the various parameters of the drilling rig. Only after strict testing and inspection, the drilling rigs that meet the requirements of various indicators can be judged as qualified products and enter the next link.
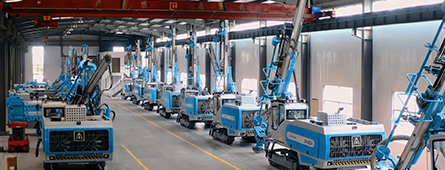
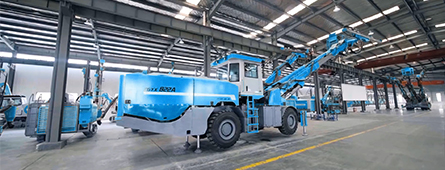
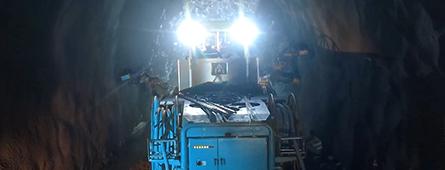
7. Appearance painting and packaging
Appearance painting: The drilling rigs that have passed the inspection are treated with appearance painting to improve the appearance and anti-corrosion performance of the drilling rigs. First, the surface of the drilling rig is pre-treated, and the rust, oil and impurities on the surface are removed by sandblasting, shot blasting, etc., so that the surface reaches a certain roughness and increases the adhesion of the coating. Then, the primer is sprayed. The primer has good anti-rust and corrosion resistance and can provide a good foundation for the subsequent topcoat. After the primer is dry, the topcoat is sprayed. The color and gloss of the topcoat are selected according to customer requirements or corporate standards. Generally, durable and weather-resistant paint is used to ensure that the appearance of the drilling rig remains good during long-term use. During the painting process, the temperature, humidity and ventilation conditions of the painting environment are strictly controlled to ensure that the painting quality meets the standards.
Packaging and transportation: Design a suitable packaging plan according to the size, weight and transportation requirements of the drilling rig. For small down-the-hole drilling rigs, wooden boxes are generally used for packaging, and cushioning materials such as foam boards and air cushion films are set in the wooden boxes to prevent the drilling rigs from being collided and damaged during transportation. For large down-the-hole drilling rigs, it may be necessary to use frame packaging or bare packaging with protection, and use professional transportation vehicles and fixing devices during transportation to ensure the safety of the drilling rig during transportation. The model, specifications, quantity, manufacturer, destination and other information of the drilling rig should be marked on the packaging to facilitate transportation and handover. At the same time, provide customers with detailed transportation lists and product certificates and other relevant documents to ensure that the drilling rig can be smoothly delivered to customers.
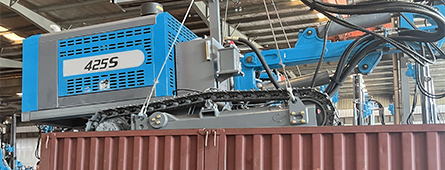
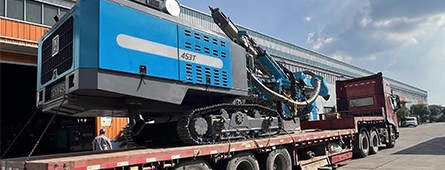
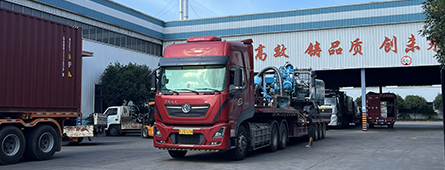
Through the above rigorous and meticulous production process, a down-the-hole drill rig with excellent performance and reliable quality was born, providing a solid guarantee for efficient operations in mining, infrastructure and other fields.